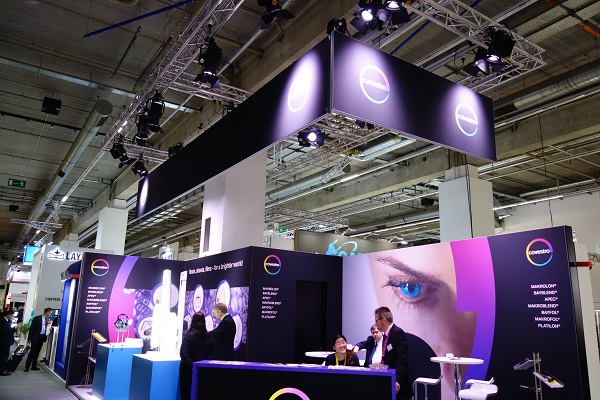 |
Covestro showcases its up-to-date polycarbonate technology at Lightig + Building 2016. (Photo Courtesy of LEDinside)
|
For new products, LED technology has become mainstream in both commercial and residential lighting. For luminaires it enables a wide range of lighting options as well as freedom of styling not possible with incandescent technology.
In recent years new materials as well as new technologies have become available to reduce luminaire complexity through component integration, which reduces part count and assembly processes.
Reflective Technologies
Most luminaires contain reflectors to achieve a specific beam pattern or lumen output. These have often been individual components of metallized or painted plastic, and in some cases polished metal. Secondary operations, such as metallization and painting, add significant cost, environmental concerns and increased scrap potential. Covestro has created a solution for these issues with Makrolon® RW2407. When injection molded, this highly reflective white material can achieve 96% reflectance in a one-step process.
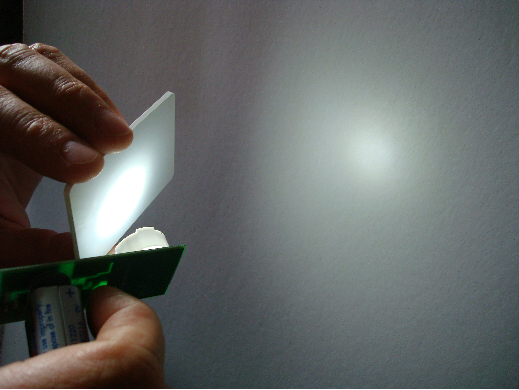
|
Makrolon® RW2407
|
The inherent high reflectivity of the part as molded eliminates the cost and risk of secondary processes. Makrolon® RW6265X utilizes the same reflective technology but also achieves the UL94 V-0 rating for applications requiring flame resistance. In addition, the technology can be applied to Bayblend® PC/ABS blends or Apec® high-heat polycarbonate for a wider selection of potential solutions.
 |
The polycarbonate technology enables improved luminaires design.(Photo Courtesy of LEDinside)
|
Integration and Material Optimization
Covestro materials such as Makrolon® RW2407 can marry reflective white technology with the design freedom of injection molding to create a single, multi-function part, such as a combined reflector and housing for a luminaire. By removing painting or metallization from the process there is no need to mask non-reflective areas making the integrated part practical with fewer process steps.
Other Covestro materials, such as the thermally conductive (TC) Makrolon® TC8010 and TC8030, make it possible to integrate electronics like printed circuit boards (PCB) directly into injection-molded parts, such as heat sinks. This eliminates assembly of the LED board to the heat sink and creates an excellent contact interface between the electronics and heat sink, removing the need for additional thermal-interface material (TIM) grease or adhesive. This avoids the cost of the TIM but may improve reliability by avoiding TIM migration or delamination caused by thermal cycling.
Material selection also plays a role with integration. For example, a material that is more costly per pound but reduces weight due to integration results in a net savings for the assembly. In other cases, savings can be realized by optimizing the use of higher-value, flame-retardant or impact-resistant grades only where needed.
To demonstrate the possible savings, a commercially available luminaire was obtained and evaluated for potential cost-saving opportunities.
Example: Commercial Downlight
A standard recessed down light, as found in a typical kitchen or office, was purchased from a large chain hardware store. Disassembly of the luminaire finds 5 major plastic components: bezel, lens, reflector, mounting plate and a top cap. A 6th major component is an aluminum housing.
Making assumptions of production volume, existing materials and utilizing cost analysis software developed by Covestro, an approximate cost to produce is estimated for the current assembly. Next, opportunities for cost reduction through integration and material selection are investigated. Although the assembly is already relatively efficient, there is potential for optimization in 3 areas:
Integration –In the current design, the reflector and trim bezel are two pieces, both made of white plastic.
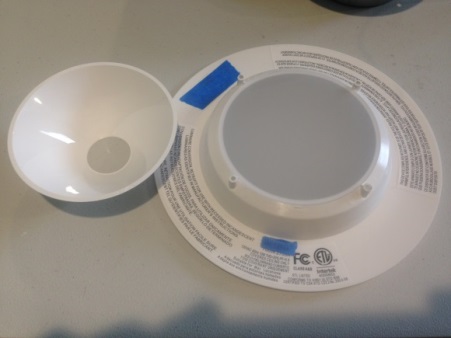
|
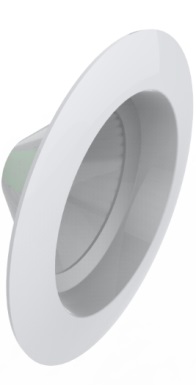
|
Current Two-Piece Design
|
One Piece Makrolon® RW2407 Bezel/Reflector
|
A few design modifications and the two-piece part can be combined into a single molded component. Cost analysis of the current and optimized design shows a potential savings of 20% through integration. This is realized in reduced tooling, cycle time, assembly and handling costs.
Material Optimization – Replacement of the die cast aluminum housing with Makrolon® TC8030 offers savings potential mainly from reduced tooling cost possible due to the longer tool life of injection molds vs. die cast.
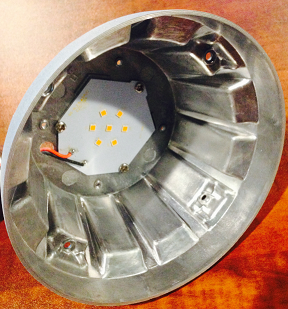
|
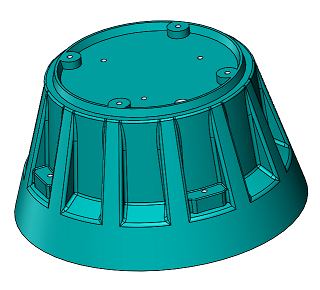
|
Current Housing
|
Makrolon® TC8030 Housing
|
Given the production volume in this analysis, a savings of 25% is possible. A large part of the savings in this case comes from the 3 injection molds vs. 11 die cast tools which would be required over a 4-year production cycle.
Molding the housing of Makrolon® TC8030 also enables integration of attachment features and the potential to mold-in the LED and driver PCBs.
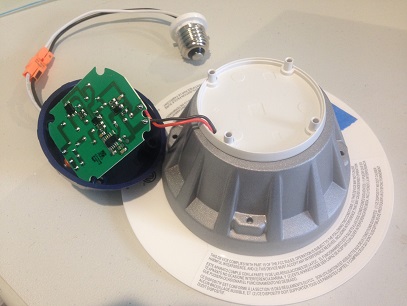
|
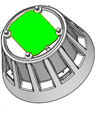
|
Current Mounting Plate
|
Integrated Mounting
|
In this design, elimination of an internal mounting plate yields an 8% reduction in the total current estimated luminaire cost.
Not every change yields cost reduction. The current top cap is a typical thermoplastic. However, in the optimized design, the cap is molded of Makrolon® TC8030 to increase thermal performance.

|
Makrolon® TC8030 Top Cap
|
The impact is an increase in cost of 89% but also a significant increase in the thermally conductive surface area.
Bottom line
Adding up the plus and minus columns shows the final tally:
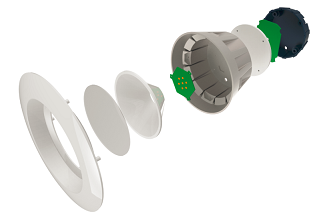
|
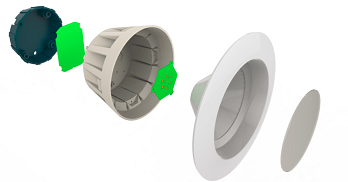
|
Current Design 8 Components
|
Optimized Design 6 components
|
The net result is a 25% reduction in components, a 43% reduction in weight and a 19% reduction in cost. These savings are based on measureable cost savings. Although not calculated, other intangible savings such as inventory cost can add to the savings.
Summary
Integration and optimization are all geared toward reduced cost. The savings from reduced tooling and labor are obvious. Of course buying less material also impacts cost, but there are benefits from buying more material from a single supplier. For example, Covestro offers clear grades, such as Makrolon® LED2245, LED2247 and LED2643 for lens or optic applications, and diffused grades to maximize LED source blocking and lumen output.
Procuring materials for reflective, thermally conductive and lens applications from Covestro can simplify logistics and allow larger volume rebates. Other benefits such as reduced inventory cost, reduction of handling and tracking multiple suppliers may be more elusive to quantify, but are nevertheless real savings.
Covestro’s material selection and know-how can help keep your designs exciting, modern and even more importantly cost efficient in this highly competitive environment.
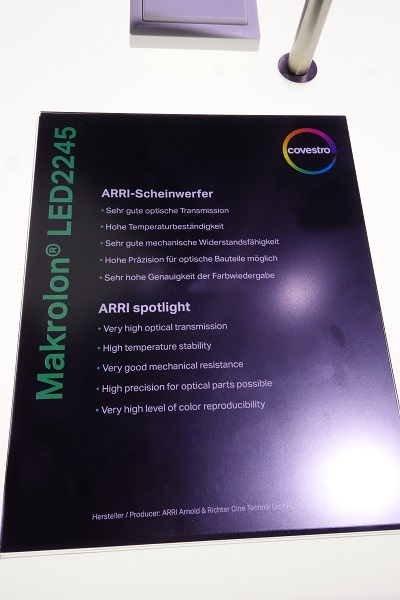 |
Makrolon® LED2245 for lens or optic applications, and diffused grades to maximize LED source blocking and lumen output.
|